|
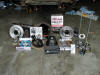 |
It's finally time to put my Dana
60 together. I've decided on a 35 spline ARB, compliments of Alex of
Performance Offroad Centers(PORC), whom I found in the vender section of
www.pirate4x4.com. I'll be using Ford
9" big bearing housing ends and 35 spline semi float 5 lug shafts. I'll also
be adding disc brakes using CJ-5 rotors and El Dorado calipers with parking
brake. Gears are a used set of 4.56. They are older gears with a course
spline pinion. |
|
I highly recommend reading
the
Dana Service Manual as well as the
Yukon Installation manual from www.ring-pinion.com Also check out my
Dana60-Teardown article.
My intent for this article is to show that the average gearhead can save a
few bucks by setting up their own gears. On the same note, I hope you'll
realize how time consuming this process can be, and why shops charge what
they do.
Setting up gears isn't rocket science. It's actually pretty simple. There
are really only 3 main steps:
1. Set pinion depth
2. Set Backlash
3. Check the pattern
Repeat these three steps until an acceptable pattern is achieved. Follow
these steps and you won't have any problems. So lets get started! |
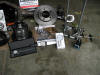 |
Some of the specialty tools required for gear
setup include:
Bearing puller
Inch pound torque wrench
Foot pound torque wrench
Dial caliper
Dial indicator with magnetic base
Pry bars
Brass drift or bearing and race installers |
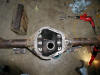 |
First things first. Clean the
housing meticulously. I use a generous amount of brake cleaner. Make sure
you clean the tubes too! Must be perfectly clean!!! |
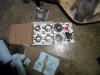 |
Timkin master install kit. Comes
with all the bearings and shims needed to put this thing together. Timkin
bearings are the top of the line. Don't settle for anything less. |
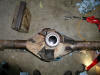 |
Now that the housing is clean we
can install the first pinion bearing race. No shims are used under this
bearing race. |
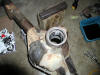 |
Since this bearing race is going
to stay put, apply a drop or two of red lock-tite and drive the bearing race
in with a brass drift. You MUST use a brass drift to avoid damaging the
bearing race. Make sure it's seated completely. |
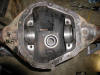 |
Next we'll install the inner
pinion bearing race. This is the main part of gear setup.....behind this
bearing race we'll place pinion depth shims. More shims moves the pinion
closer to the ring gear, less shims moves the pinion away. Of course this
means installing the bearing race, installing the pinion and carrier, then removing it
all to adjust the amount of shims. We'll be good at it by the time we're done! |
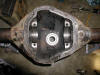 |
Included in the install kit is a
baffle. It's .020" thick and is part of the pinion depth shim pack. I'm
opting not to use this baffle and will compensate with more pinion shims. If
you choose to use it, I recommend waiting until final assembly to install
it. Otherwise you'll risk damaging it while adjusting the shim pack. The
reason I'm not using it is because of the advice of a friend. The idea is at
slower wheelin speeds the oil can flow freely through the pinion bearings.
|
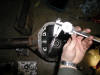 |
I couldn't find the original
shim pack from the tear down, so I really have no idea where to start. This
is where the pinion depth tool would come in handy, but it's not at all
needed. We may just have to adjust the pinion depth shims a few more times.
I heard .035" is a good place to start, plus the .020" from the baffle. So
my starting pack is .054". Check out the Dana service manual for more on
using a pinion depth tool. |
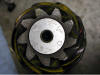 |
More on
setting pinion depth |
|
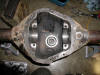 |
Place the shims in the housing.
I prefer to sandwich the thinner shims between the thicker ones. |
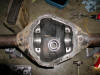 |
Again, drive the bearing race in
with a brass drift. Ensure it's completely seated. No lock-tite until final
assembly. People that do this a lot will often make a set of install
bearings and races, where they are turned down for a slip fit. Makes setup
quite a bit faster. Then for final assembly they use the new bearings and
verify the pattern is correct. |
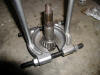 |
Now we need the pinion. But
first we need to put the new bearing on. I'm using a used set of 4.56 gears.
So first I have to remove the old pinion bearing. |
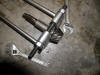 |
I'm using a bearing splitter. DO
NOT pull on the bearing cage. Make sure the splitter bites in under the main
part of the bearing. At all times you should be able to freely move the
bearing cage. I had to grind on my splitter so it would clear the bearing
cage. |
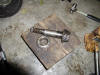 |
Old bearing removed. |
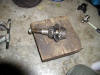 |
Also included in the master
install kit is an oil slinger. Again I'm opting not to use it, and if you'll
notice there wasn't one there originally. But if you want to use it, this is
where it would go. Keep in mind, the slinger will affect the pinion depth by
.030". I
didn't compensate for the slinger in my shim pack. I may have to
though...... we'll find out soon enough. |
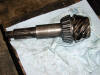 |
Cleanliness is critical. I
cleaned up the old crusty pinion with some brake cleaner and pressed on the
new pinion bearing. |
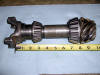 |
Now is a good time to take a
look at "Pinion bearing preload". Preload is nothing more than how
how tight the bearings are The tighter they are, the harder it will be to
turn the pinion. Very similar to adjusting wheel bearings. Pinion preload is adjusted with shims, or the
infamous "crush sleeve". in this case we're using shims. Although the master
kit included a crush sleeve. I'm not sure why? Crush sleeves suck because
they are a one time shot. If at all possible always use a crush sleeve
eliminator.
Anyhow we adjust the preload with shims. Less shims will make the bearings
tighter, and more shims will make them looser. At this point it's not
critical to get the right amount of shims. To get a better understanding,
start with a thick shim pack.....throw them all on there!
Place the pinion in the housing, then slide the outer pinion bearing on, and
then the yoke. With the yoke pressed all the way on, you'll notice the
pinion will "float" back and forth....completely sloppy! So you need to
remove shims until there is no more movement. Then remove another .005" or
so. We'll fine tune this later. I think I mine was about .070" to start.
|
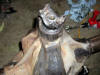 |
If you have an old pinion nut,
use it until final assembly. Go ahead and tighten it down nice and snug. The
pinion should move freely, but snug.
If you really want, you can use your
Inch pound torque wrench and fine tune the preload. Of course that would
require torqueing the pinion nut to spec. No need for that now. Also when
you change the pinion depth, the preload will need to be adjusted by an
equal amount. So don't waste your time. As long as the pinion doesn't float
back and forth, you're fine.
Seems my socket is missing. I drove all over town looking for one, but
pickings we're slim on a Sunday night. So this is where I'm stopping. Catcha
later.
I had to track down the snap-on man and buy a 1 5/16"
socket. It needs to be a thin wall socket to clear the yoke. The man charged
me about $30 ....grrrrrrr |
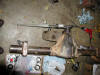 |
I have a large pipe wrench
that I use to hold the yoke while tightening the pinion nut. Many use and
impact gun, but I think doing it by hand is better, just because... |
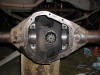 |
Almost done! |
|
[NEXT] |