|
|
The diagrams below were
copied from the www.ring-pinion.com
Yukon install manual. |
|
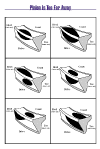 |
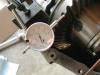 |
Here we go again........
Check backlash. I'm still a little loose at .015". Remember, when you adjust
the pinion depth, you affect backlash. I moved my pinion away, which
increased backlash. I didn't compensate enough. I'll have to add another
.010" to the ring gear side shim pack. |
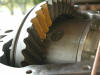 |
Once again paint a few
teeth. Technically I should get the backlash correct before checking the
pattern, but this is fun, so here goes! It helps to
mix a little oil in with the gear marking compound to thin it out a bit.
Pinion: .048"
Backlash ~.015"
Carrier, ring side: .050"
Pinion side: .023" |
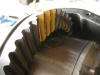 |
Ok, that sucked. Nothing really
changed. Pinion is still too deep. This is where experience comes into
play.....knowing how much of an adjustment to make. I thought I was closer
than I was. I'm going to reduce the pinion shim pack to .038" |
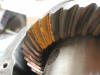 |
And the coast side. There is a
little change, but still obviously too deep. |
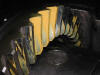 |
I expect you have the process
figured out. Removed another .010" from the pinion and added another .010"
to the carrier ring side to decrease backlash some more.
Pinion: 038"
Backlash: .010
carrier, ring side: .060"
Pinion side: .013"
Drive side: Now this is looking better. Notice how the pattern opened up
nice and broad and somewhat rounded. Still seems close to the toe of the
tooth. I'm going to remove another .005" and see what happens. |
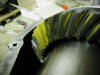 |
Again much better. The pattern
isn't as clear this time, but notice how it opened up and is taking up the
whole tooth. This is actually an acceptable pattern. However I'm going to
try and get the drive side looking a little better. |
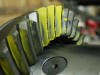 |
Pinion: 033"
Backlash: .010
carrier, ring side: .060"
Pinion side: .013"This looks pretty good. It pulled
the pattern off the toe of the tooth like I wanted. However, notice how it
got a little narrower......lets have a look at the other side. |
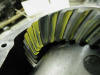 |
Not bad, but not as nice as it
was. Notice how the pattern moved to the face of the tooth (top) and toward
the toe a bit. Again, I think this is an acceptable pattern, but not good
enough for me. I'm going to add .003" back to the pinion, decrease backlash
a tad and call it good. |
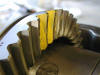 |
Whoops! I could lie and say I
did this for the sake of this write up, but no......I'm an idiot and didn't
put the pinion shim pack in. I decided to continue to show the what it might
look like if the pinion is to far away. Notice the
extreme change. The drive side pattern moved completely to the heel and top
of the tooth. |
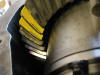 |
Again an extreme change from the
other patterns. Barely any contact at all!! |
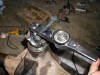 |
Since I'm getting close to a
final pattern, I dialed in the pinion bearing preload by adjusting the
preload shims. Remember the first page? A dana 60 with new bearings calls
for 17-30 in/lbs. That's quite a bit! The pinion will have quite a bit of
drag on it. Note that this is the amount of force to keep the pinion
turning, NOT the amount to get it started turning. |
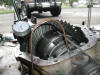 |
I decided to notch the bearing
cap so I could use it for the next pattern. I was a little concerned about
drilling/notching the bearing cap. The bearing caps are machined with the
housing, and if you ruin it, the whole housing is pretty much junk.
I read quite a few opinions on whether to drill or notch, and the
overwhelming response was to save yourself some grief and make a notch.
Unless you drilled absolutely dead on, you run the risk of snapping the
copper air line off when torqueing the bearing cap. There was talk of a
secret tool out just for this purpose, but no one said what it was. I have a
hunch it was a super secret 1/4" round file. That's what I used. Worked
great! The bearing caps are soft, and easy to file by hand. Only took me a
few minutes. I did attempt to drill first just to see how hard it would be.
I don't have a drill press. Guess what..... my pilot hole was a tad crooked.
Don't forget to chamfer the hole on the top and bottom. |
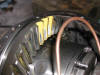 |
Pinion: 036"
Backlash: .08
carrier, ring side: .066"
Pinion side: .016"This looks pretty good. It's not
as picture perfect as I would like, but I think it will do just fine. Nice
big rounded pattern centered on the face and flank of the tooth (top and
bottom)
Keep in mind these gears were made in 1961!! They have a
few miles on them and I think the pattern reflects that. I still think they
will last forever in my bronco.
Notice I also decreased the backlash a tad and increased
the preload by adding another shim to the pinion side of the carrier. There
still isn't enough preload, so I'll be adding more shims to the pinion side
on final assembly. That will have to wait until I get the housing back from
welding on the 9" ends.
There isn't really a way to measure carrier bearing preload. The proper
method is to use a case spreader and open up the housing a tad to allow
additional shims to be added. Then once you remove the spreader, the housing
compresses on the bearings providing the bearing preload. The service manual
recommends an addition .010" for carrier bearing preload.
All I can say is you want it to be a tight fit. You shouldn't be able to
push the carrier in by hand, and you should need a pry bar to remove it. I
think it would be difficult to get too much preload without the use of a
case spreader. Keep in mind that adding additional shims for preload may
affect backlash. |
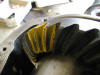 |
Again, I'm happy with this. Nice
big rounded pattern that covers a lot of the tooth. I'm calling it good.
Take note that I found the original pinion shim pack after I had finished
setting up the gears. As mentioned on the
Setting Pinion Depth
page. I determined a good starting shim pack would have been none other than
.036". Imagine that!!! |
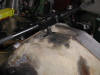 |
The ARB requires that you drill a
hole in the housing for the air line. No big deal. Make sure to clean up all
the metal shavings. The hole is 7/16" and tapped with a 1/4" pipe thread
tap. Don't go too deep with the tap. |
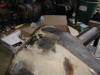 |
No problem. So far installing an
ARB hasn't been very difficult. In fact I think it's easier because
you don't have to pull one of the carrier bearings to adjust shims. |
|
Well this where I'll have
to stop until I get 9" ends welded on. See you soon! |