Page 1 of 1
Wristed Arm Inspection
Posted: Sun Oct 23, 2005 8:03 pm
by Nobody
Since I had to replace the radius arm bushings on my Bronco II, I decided to pull the wristed arm so I could inspect it. It's been nearly 4 years since I put it on. I NEVER pin the arm. It has lots of wheelin and lots of daily driving on it.
The big question everyone has, is do these things need to be greased, or need a bushing, bearing etc.....
There doesn't really appear to be any wear. There is a little bit of movement on the hinge, but I don't recall what it was like when I built it. Nothing that concerns me.
Visually, the holes are are still round, not egg shaped. Inside there aren't any signs of wear. The bolt as you can see has a couple shiney spots. Visually, I can't see or feel any significant wear.
So, take this report for what it's worth. I'll let y'all draw your own conclusions.

(NEW)
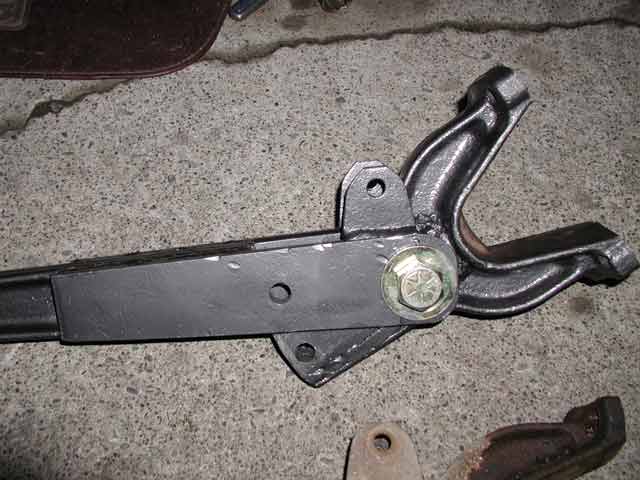
Posted: Sun Oct 23, 2005 8:33 pm
by FatMan
look's like it's been holding up..

Posted: Mon Oct 24, 2005 11:25 am
by DBrown
that does look good, I planned to check mine before it goes on the the EB this weekend. my arm was pretty snug so I am thinking it has probably loosened up from the trip last year.
Posted: Mon Oct 24, 2005 6:29 pm
by bailey
I really need to get off my butt and get a real welder so as to do that.
It annoys the hell out of me when I go to your main page and see your rig there, with like a bazillion times more flex than my B2 (aka Mr. Stiffy).
But the garage in my brand-new house doesn't have 220V. And my laundry room w/ 220 is upstairs (real estate agent actually used that as a selling point - "it's where the laudry accumulates" -

).
Seriously looking at getting a Ready Welder.
Posted: Mon Oct 24, 2005 6:38 pm
by ranger5.0
Looks like it is holding up pretty well for a ford part. Good work

Posted: Mon Oct 24, 2005 7:11 pm
by Nobody
bailey wrote:I really need to get off my butt and get a real welder so as to do that.
It annoys the hell out of me when I go to your main page and see your rig there, with like a bazillion times more flex than my B2 (aka Mr. Stiffy).
But the garage in my brand-new house doesn't have 220V. And my laundry room w/ 220 is upstairs (real estate agent actually used that as a selling point - "it's where the laudry accumulates" -

).
Seriously looking at getting a Ready Welder.
I had to run 220V to my garage. Had to put 220V in my old duplex too.It really wasn't that big of a deal. Where is your breaker box? I doubt it's upstairs. It's pretty easy to drop down from the breaker box into the crawl space and over to the garage.
Definately get that wristed arm done. It makes all the difference. Extended arms is another option if fabbing a wristed arm is out. That's going to cost you though.
If you invest in a welder it really should be 220V
Posted: Mon Oct 24, 2005 8:49 pm
by bailey
I still have a cheap Cambell-Hausfield 115 that I bought ~5 years ago. I used it for a lot of the d44 swap, but after tacking the leaf spring perches on and tacking the trac bar bracket together with the little welder, I took those things to a shop and had a real welder finish them. I know for a fact the 115 wouldn't be appropriate for the wristed arm project, no matter how much prep-work and beveling I do. Also, I have a hard time making mutiple passes look decent, without grinding the heck out of the welds.
I was talking with a guy that had a Ready Welder (basically, a MIG spool gun that you hook up to 2-3 12V batteries, ~400 bucks), and he had no problem with 1/2" + penetration (using flux-core for that thickness, I think). I would prefer a big Miller or Lincoln for sure, though.
But I'll get the wristed arm done this winter for sure.
Posted: Tue Oct 25, 2005 4:59 am
by DBrown
my lincoln 225 was only a little over $200 at lowes. it is an arch welder but for suspension parts it works well.